炭黑对轮胎胎面抗切割和抗碎裂性能的影响
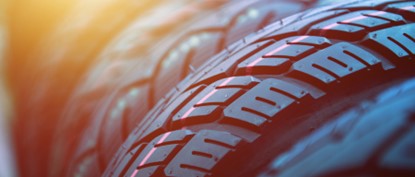
使用中的轮胎胎面磨损是更换轮胎的主要原因,可能会导致个安全问题。从广义上讲,胎面磨损可分为两类:
· 磨蚀性/热氧化性磨损。这种磨损的特点是,由于驾驶时遇到的摩擦力加上正常的环境暴露,胎面逐渐脱落。这种形式的磨损是最为常见的。
· 切割和碎裂磨损。这种类型的磨损在非公路应用中很常见。路面上的尖锐、大型的突起物会割伤胎面。然后,随着轮胎的持续使用,割伤的部分会被撕掉,成为一大块碎屑。
需要最强抗切割和抗碎裂性能的轮胎是那些在恶劣环境下运行的轮胎。例如,直径为15-20英尺的巨型挖土机轮胎,压过尖锐农作物秸秆的大型联合收割机轮胎,或在尖锐碎石上运行的更常见的自卸卡车轮胎。
炭黑如何影响抗切割和抗碎裂性能
切削和碎裂磨损现象很复杂,它与正常的路面磨损截然不同。我们面临的挑战是如何理解和优化那些有影响的参数。从炭黑的角度来看,通常可以从三个方面提高橡胶复合物的抗切割和碎裂性能:表面积、结构和表面活性。
表面积:高细度等级可形成橡胶分子可以与之结合的更大表面积。这导致了高能量耗散,为裂纹尖端或撕裂继续扩大制造了障碍。
表面活性:这指的是炭黑表面的挥发性氧基团的水平。炭黑的表面活性越低,或者说表面更 "死",橡胶分子就可以更加自由地移动,并在炭黑表面滑动,产生摩擦。这种摩擦也是能量耗散的来源,可延缓裂纹或撕裂的扩大。
结构:结构等级较低,就会大大增加内在的撕裂强度。与表面积和表面活性相比,人们对这一现象背后的确切机制还不太清楚。一种解释是,结构等级越低,被困在填料聚集体中的橡胶数量就较少,这使得复合物在断裂前的拉伸更长。这是优化"韧性"的一种方法。
橡胶复合物的平衡法
实际上,针对提高抗切割和碎裂的配方还包括平衡其他属性。例如,软质复合物非常容易受到磨蚀性磨损。因此,主要用于软土的农业轮胎的解决方案可能与需要在水泥路上行驶的自卸卡车的解决方案大不相同。
我们还必须考虑到为了环境可持续性而减少排放的迫切需要。如上所述,增强抗撕裂性的主要机制是增加能量耗散。高能量耗散与高滚动阻力和低燃油效率直接相关。高能量耗散还与轮胎中的热积聚有关,这对耐磨性产生继发性影响。